Hand Laser Weld: Precision Welding for Modern Applications
Hand laser weld technology has transformed precision welding, delivering unparalleled efficiency, strength, and versatility. As industries evolve, this innovative approach to welding addresses the need for accuracy, reliability, and speed in various applications.
What Is Hand Laser Weld Technology?
Hand laser weld technology uses a high-intensity laser beam to join materials, typically metals. Unlike traditional welding techniques, it offers localized heat application, minimal distortion, and superior weld quality, making it ideal for intricate and delicate tasks.
Advantages of Hand Laser Weld
1. Exceptional Precision
Hand laser welding ensures clean and accurate joints, reducing the need for post-weld machining.
2. Versatility Across Materials
This technology is compatible with a wide range of metals, including stainless steel, aluminum, and alloys.
3. Minimal Heat Affected Zone (HAZ)
The focused heat application prevents warping or distortion in surrounding areas.
4. Enhanced Efficiency
Its high-speed operation reduces production time without compromising quality.
5. Portability
Unlike large, stationary welding machines, hand laser welders are lightweight and portable, making them ideal for on-site applications.
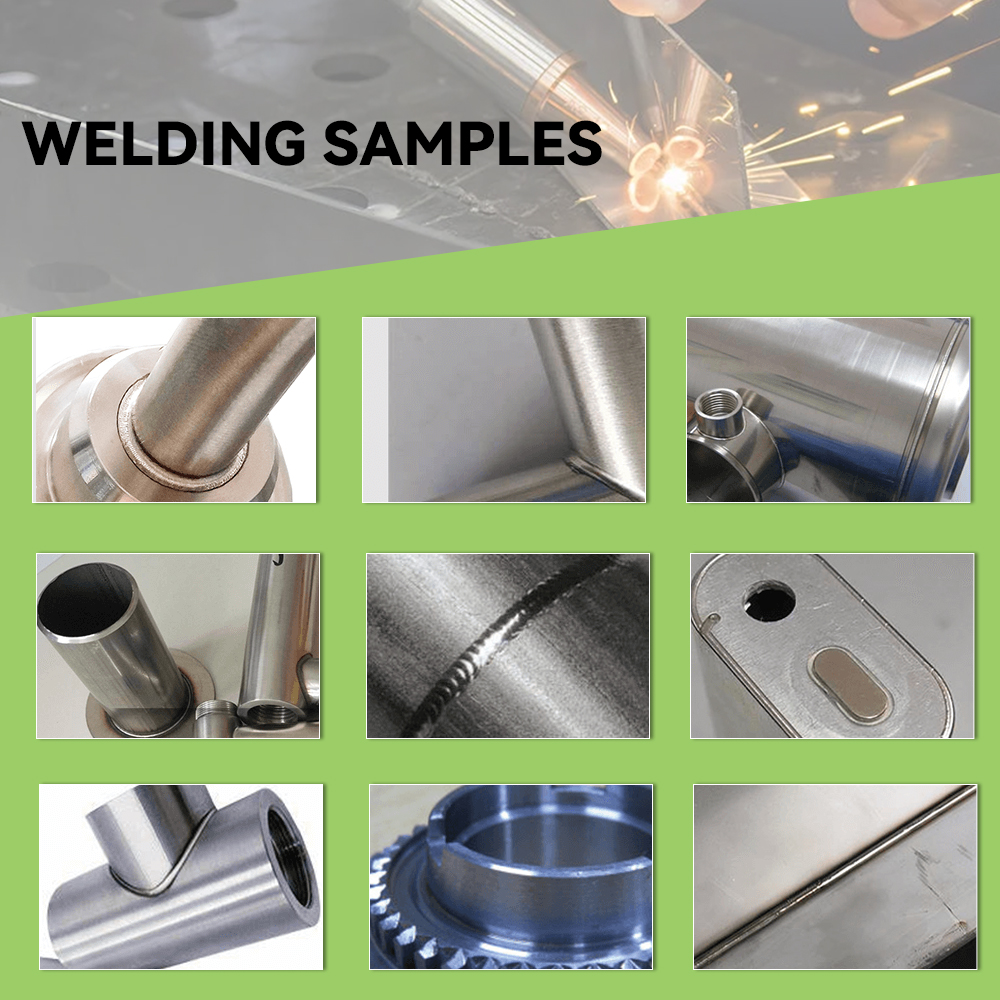
Applications of Hand Laser Welding
1. Automotive Industry
Used for repairing car frames, exhaust systems, and intricate components.
2. Jewelry Making
Enables precision welding for delicate materials like gold and silver, preserving intricate designs.
3. Medical Devices
Creates strong, sterile joints in surgical instruments and implants.
4. Aerospace Engineering
Used for lightweight, high-strength welding in aerospace components.
5. Electronics
Facilitates the assembly of compact electronic parts with precision.
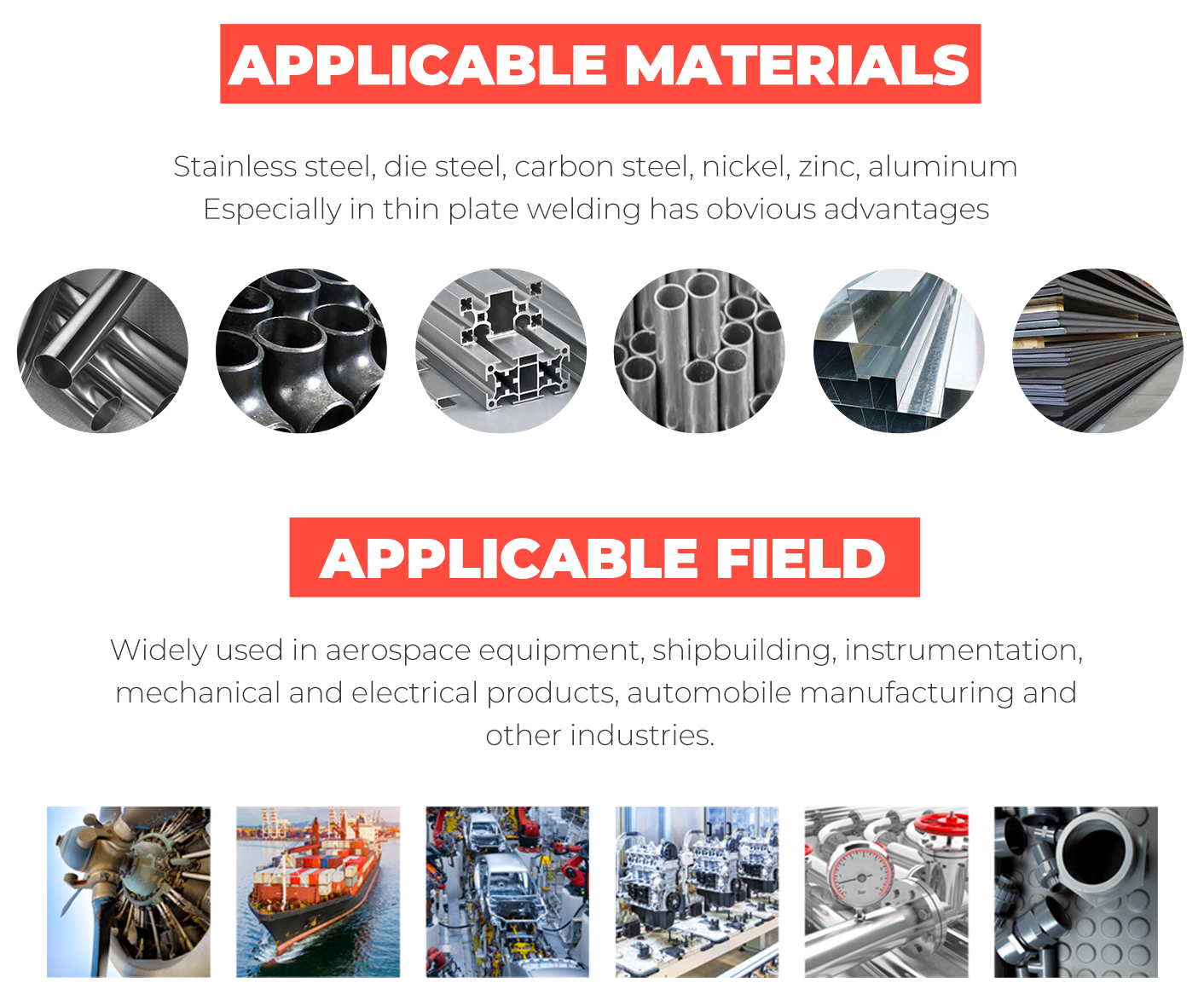
Key Features of Hand Laser Weld Technology
1. Fiber Laser Integration
The use of fiber lasers ensures high energy efficiency and superior beam quality.
2. Adjustable Power Levels
Customizable settings allow users to optimize welding parameters for different materials and thicknesses.
3. Easy-to-Use Interface
User-friendly controls make hand laser welders accessible to professionals and beginners alike.
4. Real-Time Monitoring
Advanced systems offer real-time feedback, ensuring consistent weld quality.
How to Optimize Hand Laser Welding
1. Proper Surface Preparation
Ensure that materials are clean and free from contaminants before welding.
2. Parameter Adjustments
Adjust power, speed, and focus to match the specific requirements of each project.
3. Practice on Test Materials
Experiment with scrap pieces to fine-tune settings and achieve desired results.
4. Use Protective Gear
Always wear appropriate safety equipment to prevent exposure to laser beams and fumes.
Innovations in Hand Laser Weld Technology
1. AI-Powered Welding Systems
Artificial intelligence is being integrated to enhance precision and automate parameter adjustments.
2. Compact and Ergonomic Designs
Modern hand laser welders are designed to reduce user fatigue during prolonged use.
3. Advanced Cooling Systems
Improved cooling mechanisms prevent overheating and extend the lifespan of the equipment.
4. Integration with IoT
Internet of Things (IoT) connectivity allows remote monitoring and diagnostics.
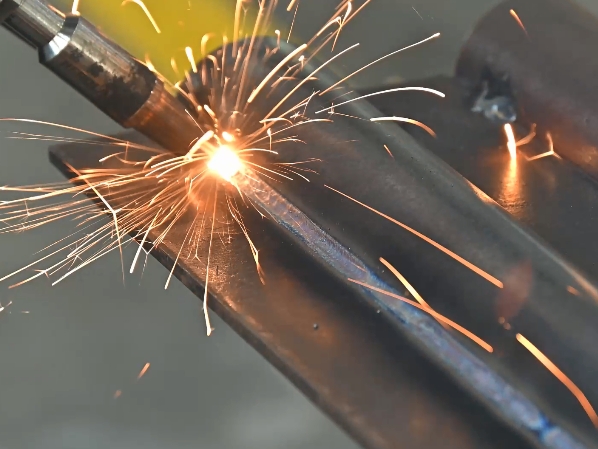
Challenges in Hand Laser Welding
1. High Initial Investment
The cost of hand laser welders may be higher compared to traditional welding equipment.
2. Learning Curve
Operators require training to master the technology and maximize its potential.
3. Maintenance Requirements
Regular maintenance is essential to ensure consistent performance and longevity.
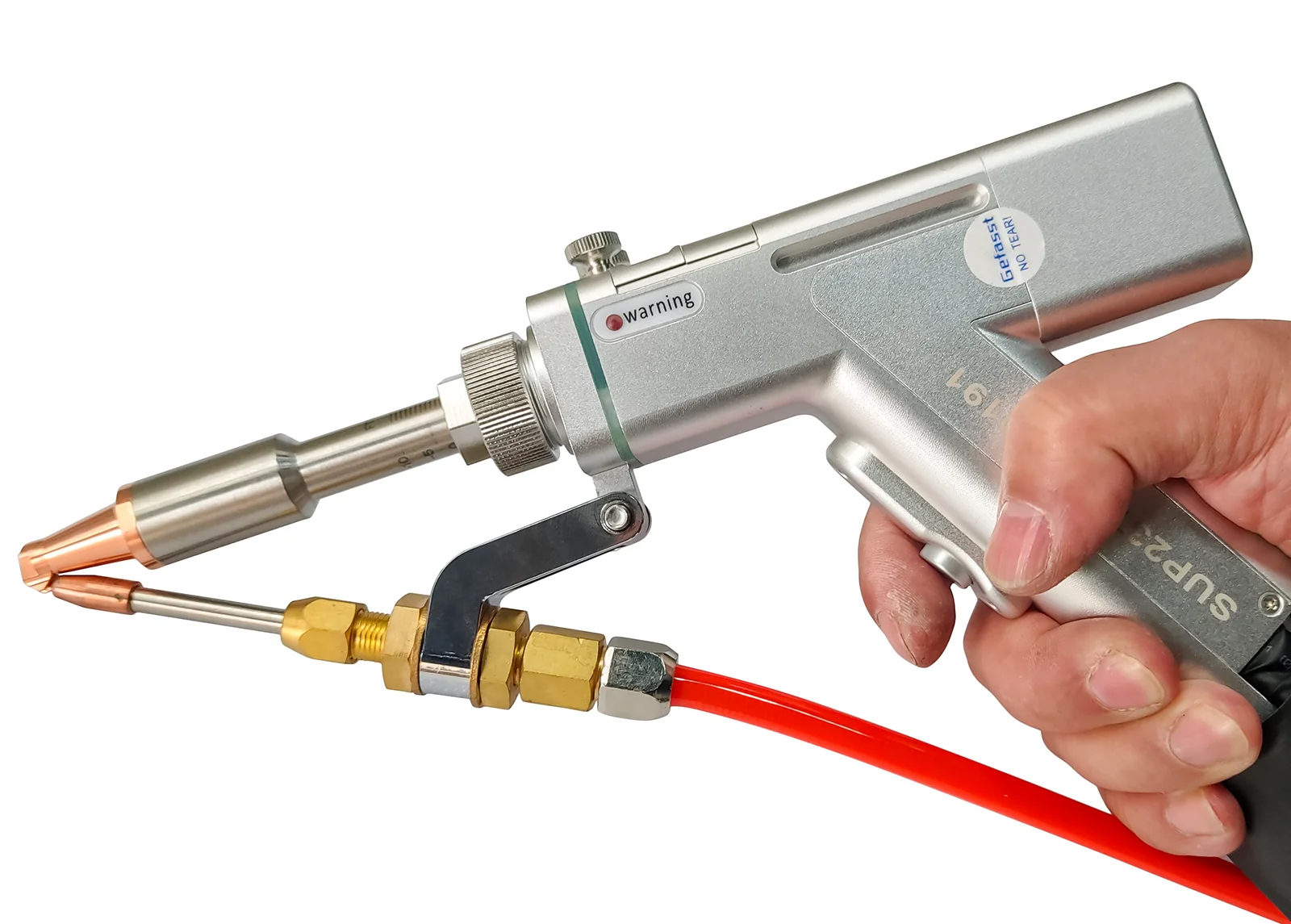
Comparing Hand Laser Welding with Traditional Methods
Feature | Hand Laser Weld | Traditional Welding |
---|---|---|
Precision | High | Moderate |
Heat Distortion | Minimal | Significant |
Speed | Faster | Slower |
Portability | Portable | Stationary |
Material Range | Wide | Limited |
Economic and Environmental Benefits
1. Cost Efficiency
While the initial cost of hand laser welders may be high, their efficiency reduces overall production costs in the long run.
2. Sustainability
Hand laser welding minimizes material waste and energy consumption, aligning with green manufacturing practices.
3. Productivity Gains
The speed and accuracy of hand laser welders enhance throughput, reducing downtime and errors.
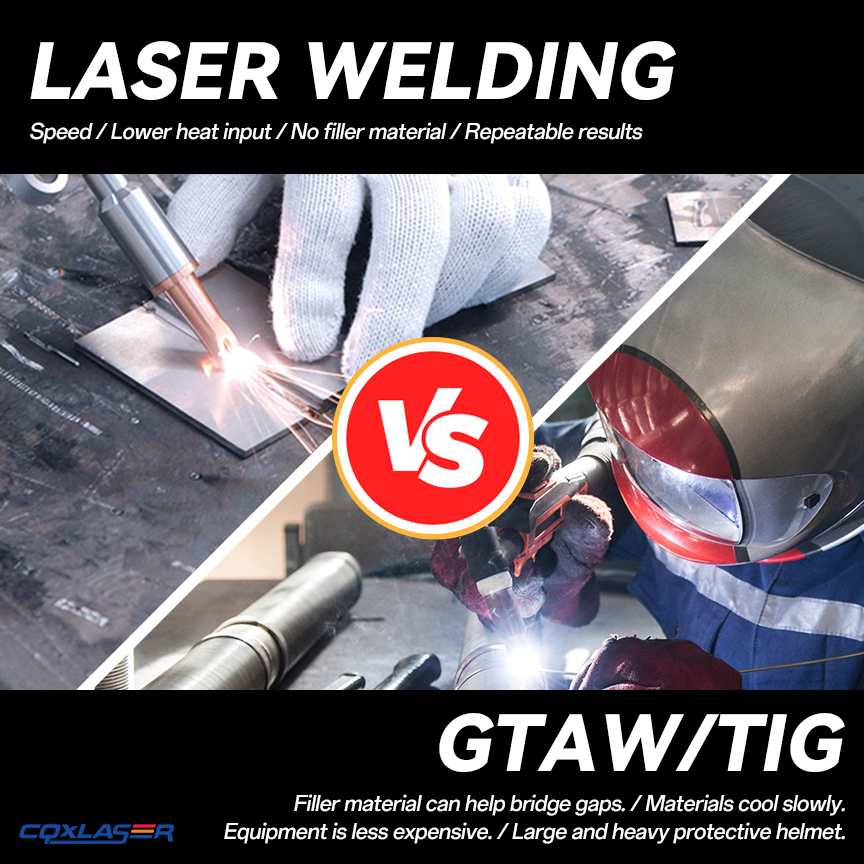
Future Trends in Hand Laser Welding
1. Autonomous Welding Systems
Fully automated systems will streamline operations, reducing the need for manual intervention.
2. Enhanced Beam Control
Innovations in beam control will allow for even greater precision in intricate applications.
3. Expanded Material Compatibility
Future systems will accommodate challenging materials, broadening the scope of applications.
4. Collaborative Robotics
Robotic systems equipped with hand laser welders will work alongside human operators, increasing efficiency and safety.
Closing Insights
Hand laser welding has redefined the possibilities in precision joining, offering unparalleled benefits across industries. By understanding its capabilities, applications, and advancements, businesses can make informed decisions and stay ahead in the competitive landscape. This technology is not just a tool—it’s a revolution in the world of welding. Explore its potential today and see how it can transform your processes.