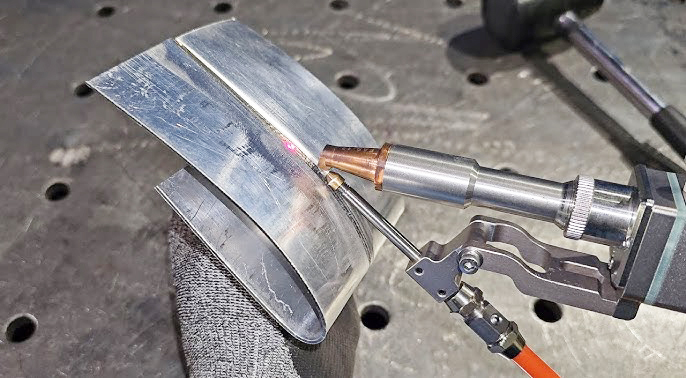
Aluminum Laser Welding: Precision, Efficiency, and Applications
Aluminum laser welding has redefined the standards of precision and efficiency in modern manufacturing. Known for its ability to create seamless and durable joints, this technique is revolutionizing industries that demand accuracy and strength. From automotive to aerospace, the applications of laser welding for aluminum are vast and impactful.
Understanding Aluminum Laser Welding
Aluminum laser welding involves using a high-energy laser beam to fuse aluminum parts. Unlike traditional methods, this process ensures minimal distortion and exceptional weld quality. Its precision makes it an ideal choice for intricate designs and critical applications.
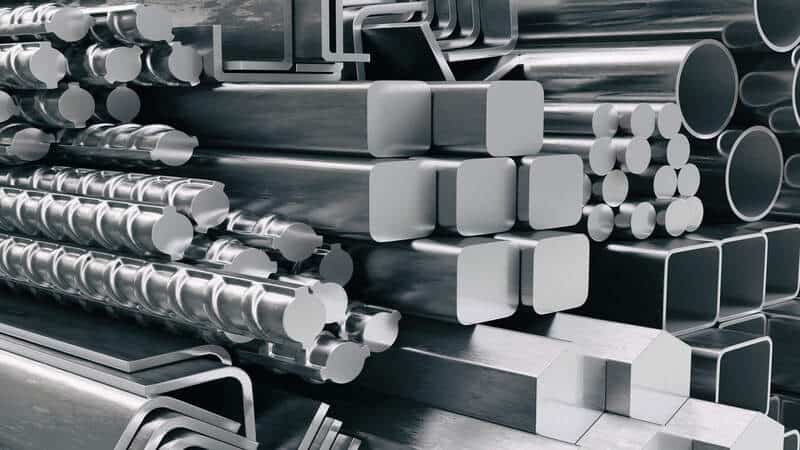
Why Choose Aluminum Laser Welding?
1. Superior Precision
Laser welding produces cleaner and more accurate joints compared to other welding methods. This precision reduces the need for additional finishing processes.
2. Faster Production
The speed of aluminum laser welding allows manufacturers to meet tight deadlines without compromising quality.
3. Minimal Heat Distortion
The concentrated laser beam limits heat spread, preserving the integrity of the surrounding material.
4. High Strength and Durability
Welds created through this process exhibit exceptional strength, ensuring long-lasting results.
5. Environmentally Friendly
With minimal waste and reduced energy consumption, aluminum laser welding aligns with sustainable manufacturing practices.
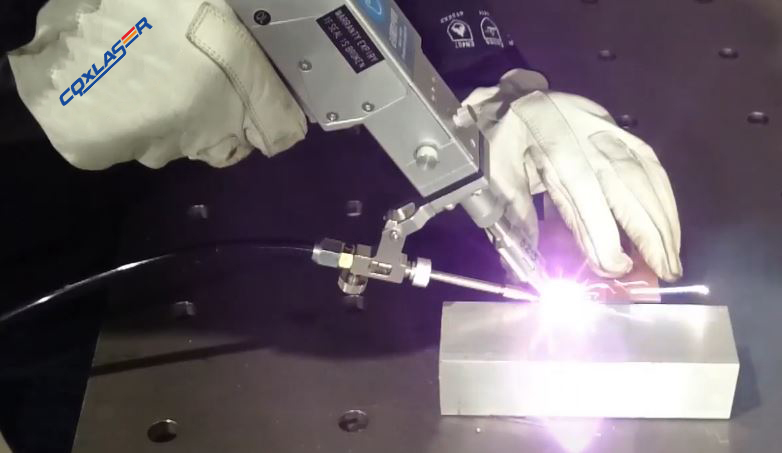
Applications of Aluminum Laser Welding
1. Automotive Industry
In car manufacturing, aluminum laser welding is used for body panels, structural components, and battery casings for electric vehicles.
2. Aerospace Engineering
The lightweight properties of aluminum combined with the strength of laser welds make it ideal for critical aerospace components.
3. Electronics
In electronics manufacturing, laser welding is employed to assemble compact and precise parts, ensuring functionality and durability.
4. Renewable Energy
Wind turbines and solar panels often use laser-welded aluminum parts for strength and longevity.
5. Construction and Architecture
Laser welding provides the precision needed for complex aluminum structures in modern architectural designs.
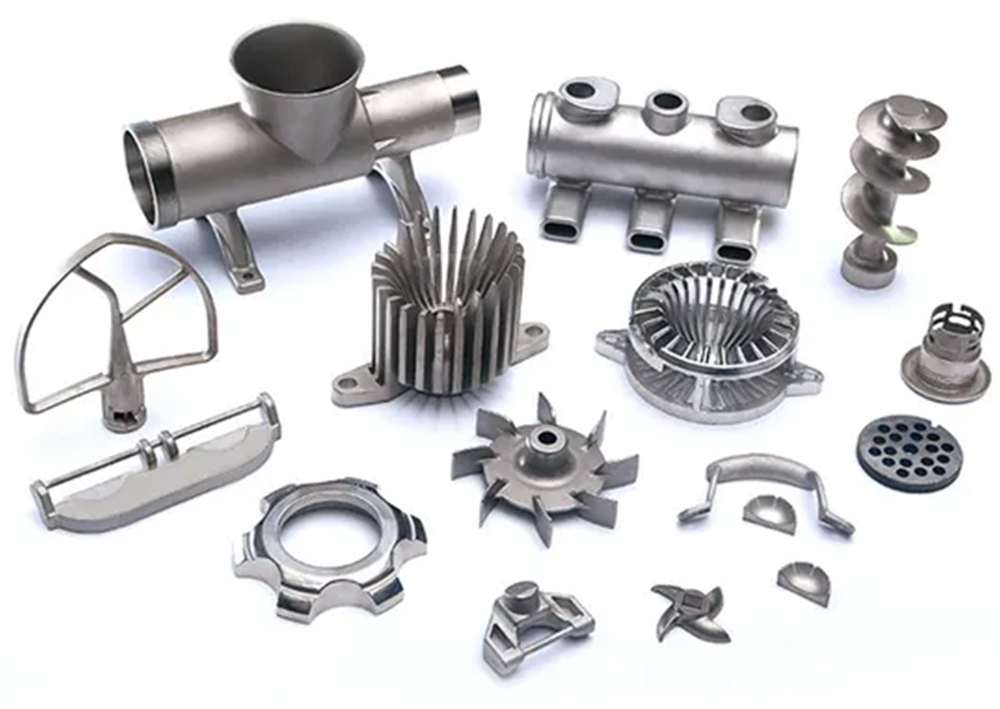
Challenges in Aluminum Laser Welding
1. Reflectivity
Aluminum’s high reflectivity can affect the efficiency of laser absorption, requiring advanced laser systems for effective welding.
2. Thermal Conductivity
Aluminum’s high thermal conductivity can dissipate heat quickly, making it essential to optimize laser parameters for consistent welds.
3. Oxide Layers
The natural oxide layer on aluminum surfaces must be removed to ensure strong weld bonds.
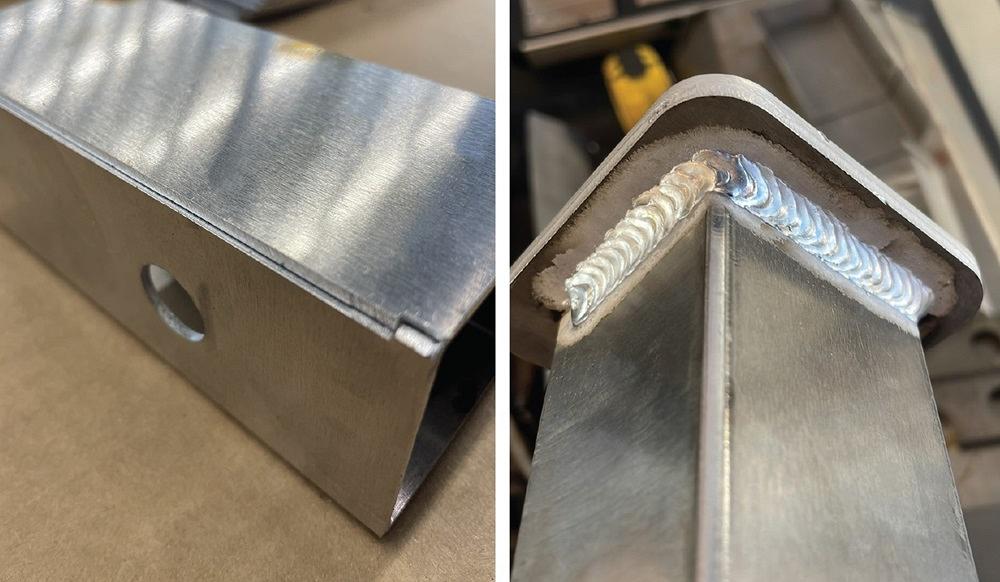
Key Techniques in Aluminum Laser Welding
1. Pulsed Laser Welding
Ideal for thin aluminum sheets, pulsed laser welding reduces heat input while maintaining precision.
2. Continuous Laser Welding
This technique is suited for thicker materials, ensuring deep penetration and strong joints.
3. Hybrid Laser Welding
Combining laser welding with traditional methods enhances efficiency and weld quality for challenging applications.
How to Optimize Aluminum Laser Welding
1. Use Advanced Laser Systems
High-quality fiber lasers improve precision and reduce the impact of reflectivity.
2. Optimize Welding Parameters
Adjusting power, speed, and focus ensures consistent weld quality across different aluminum grades.
3. Surface Preparation
Cleaning aluminum surfaces before welding eliminates contaminants and oxide layers.
4. Implement Real-Time Monitoring
Advanced systems with sensors can monitor weld quality and make adjustments in real-time.
Innovations in Aluminum Laser Welding
1. AI-Driven Welding Systems
Artificial intelligence enhances precision by analyzing real-time data and optimizing parameters.
2. High-Power Fiber Lasers
The development of high-power lasers enables faster and more efficient welding for thick aluminum parts.
3. Automated Welding Solutions
Robotic systems increase productivity while maintaining consistent quality.
4. Enhanced Cooling Systems
Advanced cooling mechanisms prevent overheating and extend machine lifespan.
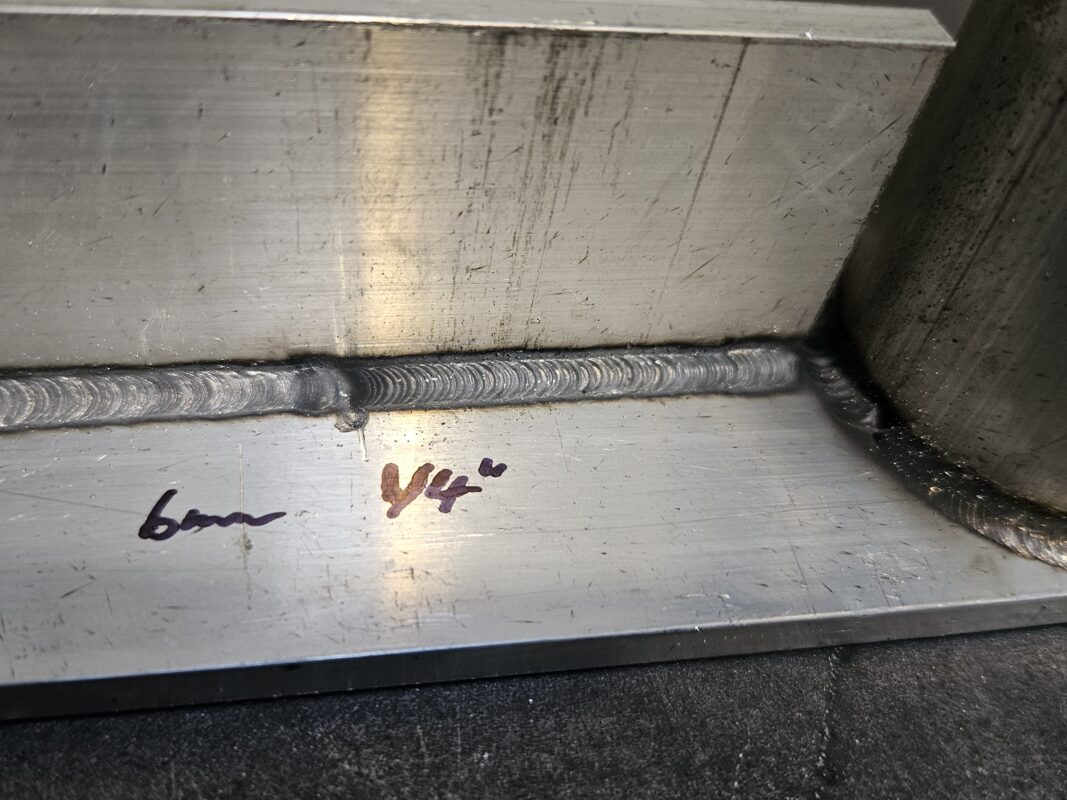
Comparing Aluminum Laser Welding with Traditional Methods
Feature | Laser Welding | Traditional Welding |
---|---|---|
Precision | High | Moderate |
Speed | Faster | Slower |
Heat Distortion | Minimal | Significant |
Material Compatibility | Wide Range | Limited |
Durability | High | Moderate |
Economic and Environmental Benefits
Cost Savings
While the initial investment for laser welding equipment may be high, the long-term benefits, including reduced material waste and labor costs, outweigh the expense.
Sustainability
Laser welding minimizes energy consumption and reduces waste, aligning with eco-friendly manufacturing standards.
Enhanced Productivity
The speed and precision of laser welding lead to higher production rates and fewer defects, improving overall efficiency.
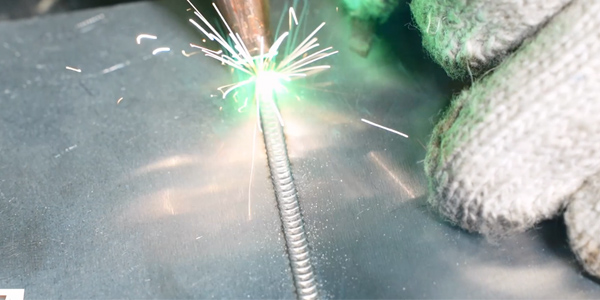
Future Trends in Aluminum Laser Welding
1. Portable Laser Welding Machines
Compact and portable designs make it easier to perform on-site aluminum welding.
2. Advanced Beam Shaping
New techniques in beam shaping allow for greater control over heat distribution, enhancing weld quality.
3. Collaborative Robots
Robots equipped with laser systems can work alongside humans, increasing safety and efficiency in manufacturing environments.
4. Expanded Material Compatibility
Research is ongoing to improve laser welding capabilities for challenging aluminum alloys.
Final Thoughts
Aluminum laser welding represents the pinnacle of precision and efficiency in modern manufacturing. With its ability to meet the demands of various industries, this technology is paving the way for innovations in design, production, and sustainability. By understanding the techniques, applications, and benefits, businesses can make informed decisions and leverage the full potential of aluminum laser welding.
Explore this revolutionary welding solution and see how it can transform your manufacturing processes for the better.