Unlocking the Potential of Fiber Optic Laser Welding
Fiber optic laser welding stands at the forefront of precision manufacturing, offering unmatched efficiency and adaptability across industries. Whether it’s aerospace, medical devices, or automotive production, this technology is reshaping how materials are fused with precision. In this detailed guide, we’ll explore the mechanics, benefits, and wide-ranging applications of fiber optic laser welding, giving you a comprehensive understanding of its transformative potential.
The Fundamentals of Fiber Optic Laser Welding
What is Fiber Optic Laser Welding?
Fiber optic laser welding uses a concentrated laser beam delivered through a fiber optic cable to fuse materials. This method ensures high precision, reduced heat-affected zones, and a strong weld joint, making it ideal for intricate applications.
How Does It Work?
1. Laser Beam Generation: The laser source emits a beam of light.
2. Beam Delivery: A fiber optic cable transfers the laser to the welding point.
3. Material Fusion: The concentrated energy melts the materials, forming a strong joint as they cool.
Why Choose Fiber Optic Laser Welding?
Fiber optic laser welding offers unparalleled advantages that make it a go-to solution for industries seeking efficiency and precision.
• High Precision: Perfect for small, intricate components.
• Speed and Efficiency: Faster than traditional methods, reducing production time.
• Material Versatility: Works on metals, polymers, and composite materials.
• Reduced Heat Damage: Minimal distortion and heat-affected zones.
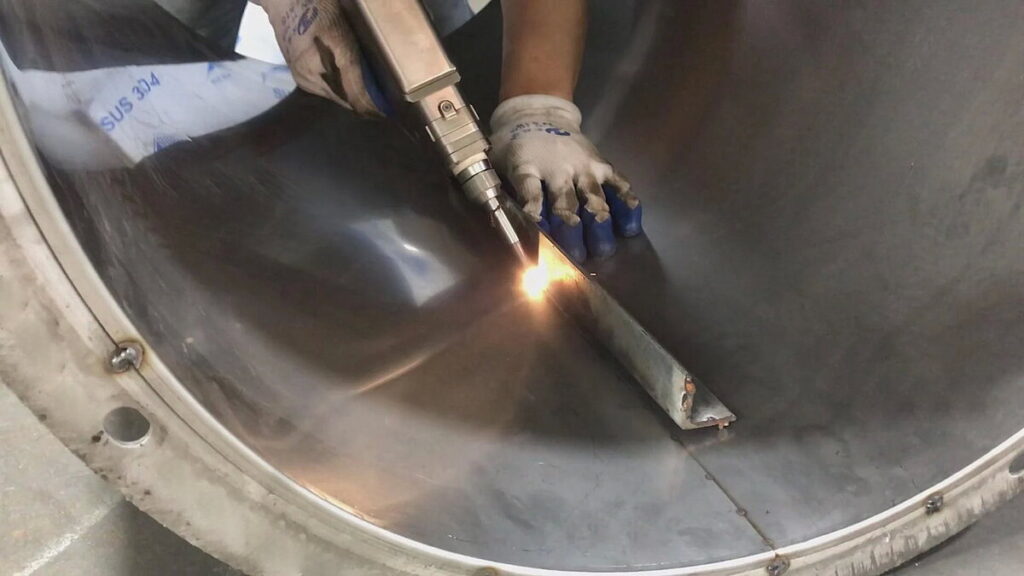
Key Applications of Fiber Optic Laser Welding
Aerospace Engineering
Fiber optic laser welding ensures durability and precision in assembling aircraft components, where safety and performance are paramount.
Medical Devices
From surgical instruments to implants, the technology guarantees the hygiene and accuracy needed in the medical field.
Automotive Manufacturing
Fiber optic laser welding is used to create lightweight, durable parts that enhance vehicle performance and fuel efficiency.
Electronics
The precision of this welding method is ideal for delicate electronic components, ensuring reliable connections without damaging sensitive parts.
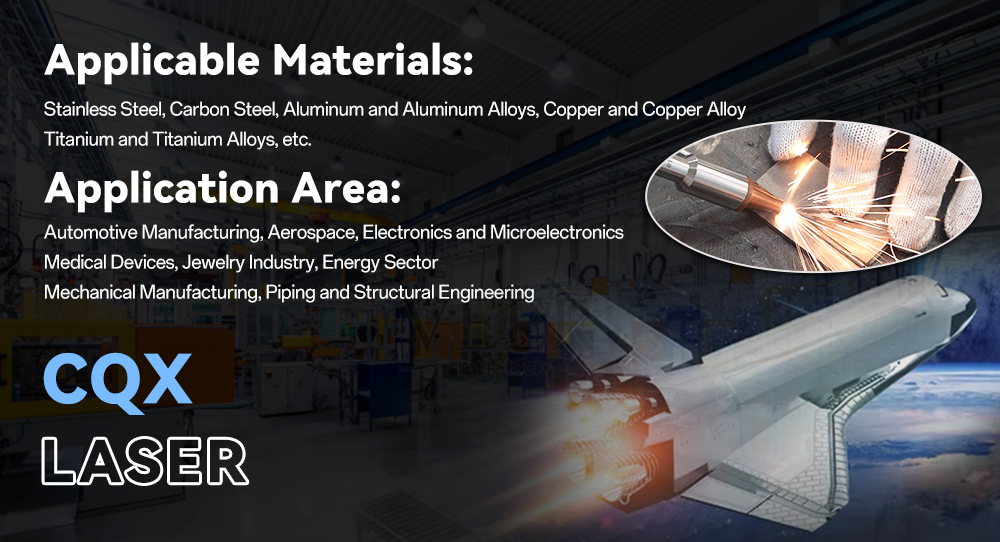
Factors Affecting Fiber Optic Laser Welding Costs
Equipment Complexity
Advanced systems with high customization capabilities typically come at a higher cost.
Material Type
The nature of the material being welded—its thickness, composition, and reflectivity—impacts the process’s efficiency and cost.
Production Volume
Higher production demands may necessitate more robust equipment, increasing upfront investment but lowering per-unit costs.
Maintenance Needs
Regular maintenance, including fiber cable inspection and laser source calibration, adds to long-term expenses.
Advantages Over Traditional Welding Methods
Greater Precision
Fiber optic laser welding allows for micron-level accuracy, essential for industries like electronics and medical devices.
Lower Energy Consumption
Compared to arc welding, fiber lasers consume significantly less power, reducing operational costs.
Clean Welding Process
Minimal emissions and material wastage make this method environmentally friendly.
Scalability
Easily integrates with automated systems for mass production, ensuring consistent results at scale.
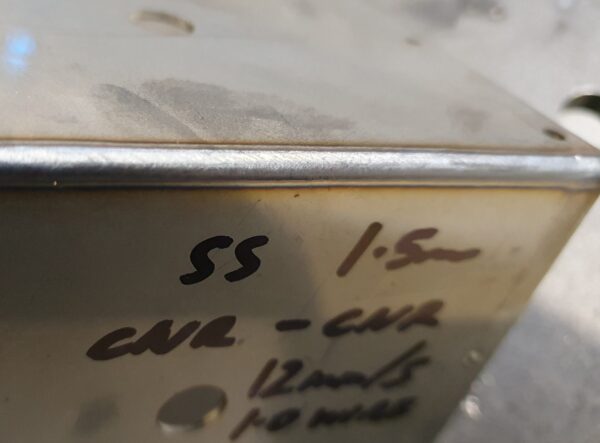
Emerging Trends in Fiber Optic Laser Welding
AI Integration
Artificial intelligence enhances process control, improving weld quality and reducing errors.
Green Manufacturing
Sustainable practices are driving the adoption of energy-efficient laser welding systems.
Compact Designs
Portable and compact systems are becoming popular for field applications.
Customization
Tailored solutions for specific industry needs are on the rise, enabling higher efficiency and performance.
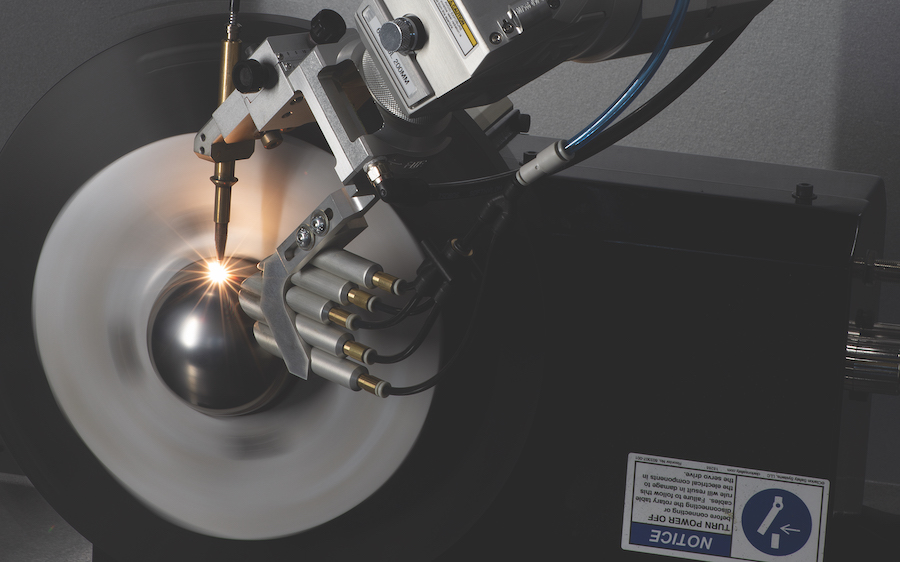
How to Maximize the Benefits of Fiber Optic Laser Welding
1. Choose the Right Equipment: Invest in systems that align with your production needs.
2. Train Your Team: Proper training ensures efficient operation and minimizes errors.
3. Implement Regular Maintenance: Keep equipment in optimal condition to avoid costly downtime.
4. Monitor Performance: Use advanced software tools to track and optimize the welding process.
Future Prospects
The demand for fiber optic laser welding continues to grow as industries prioritize precision, speed, and sustainability. Innovations in laser technology, coupled with increasing affordability, are making this advanced welding method accessible to businesses of all sizes.
Fiber optic laser welding is more than just a technological advancement; it’s a revolution in how we approach manufacturing challenges. By understanding its applications, benefits, and potential, businesses can harness this technology to stay competitive in a rapidly evolving market.